Le eccezionali caratteristiche del basalto fuso nascono da materiali antichi milioni di anni e da straordinari procedimenti produttivi:
- – la lava di basalto viene estratta da giacimenti di basalto
- – quindi viene frantumata meccanicamente in pezzi grossi come un pugno,
- – viene quindi portata alla temperatura di fusione di circa 1.300 °C,
- – viene colata in stampi metallici di forma e dimensioni prestabilite
- – gli elementi vengono sottoposti ad un processo di raffreddamento di 3 giorni in un forno che porta lentamente latemperatura da 950 °C a 100 °C,
- – si ottengono così le straordinarie mattonelle dall’inimitabile naturale e particolare colorazione.
La lavorazione ha radici nell’antico lavoro artigianale di fusione e si esalta nel creare un prodotto autenticamente naturale, ricco di storia e di tradizione, impreziosito da lati spontaneamente irregolari, con piccoli inserti e irregolarità superficiali, piccole fessure, pori e impronte della fusione a mano, propri di questo materiale unico nell’aspetto e genuino nei contenuti. I prodotti in basalto fuso sono incombustibili, inesplosivi e non rilasciano sostanze tossiche o nocive, e sono caratterizzati da una elevate densità (2,9-3,1 g/cm3).
Il colore scuro agevola, anche con il minimo raggio di sole, l’eliminazione delle formazioni di ghiaccio ed il prosciugamento delle superfici non assorbenti.
Mediante la combinazioni di tipi diversi di selciato è consigliato l’impiego come riferimento per le persone non vedenti.
Il peso del materiale è calcolato facendo riferimento al valore standard di circa 2.960 kg/m3: il calcolo è approssimativo perchè la massa effettiva può variare per composizione e per il tipo di scanalature del retroattacco.
Un riscaldamento lento con incremento di circa 60 °C/ora permette l’impiego del basalto fuso in ambienti con temperature fino a 350 °C: è il prodotto ideale per il riscaldamento a pavimento, anche di aree esterne.
L’elevata resistenza all’usura, alla compressione, all’attacco chimico del basalto fuso sono conseguenza della cristallizzazione derivante la fusione a 1.300 °C, al raffreddamento controllato, al passaggio nel forno di raffreddamento e stabilizzazione per un tempo minimo di 3 giorni.
Superfici pavimentate con mattonelle di basalti tipo Metropan 1 e Metropan 2 sono adeguate per ambienti con molto traffico o carrabili e per spazi aperti, dove è necessario garantire resistenza, durata e resistenza antiscivolo.

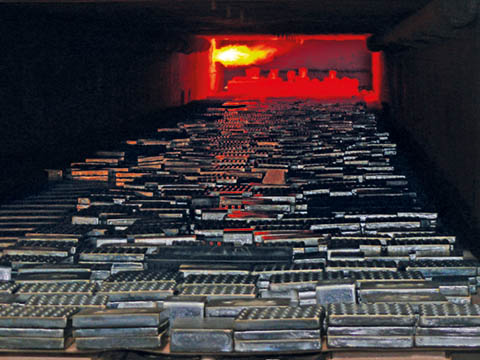
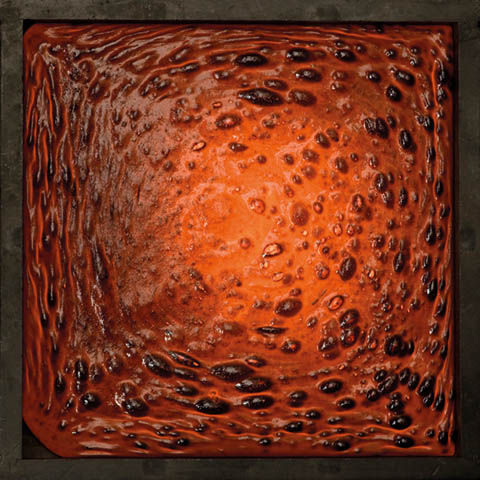
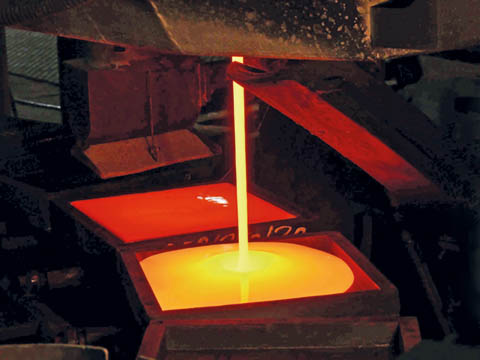
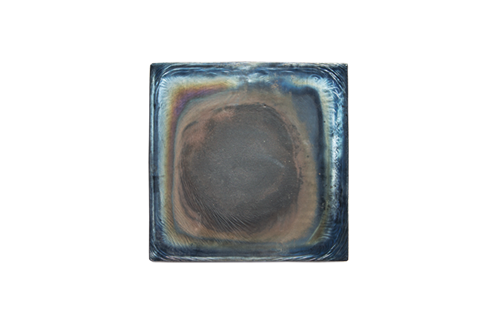
Fornitura di mattonelle e pezzi speciali coordinati in basalto, realizzati attraverso fusione e colaggio di materie prime con composizione mineralogica costituita da silice, magnetite, olivine, pirosseno, plagioclasio, anfibolo, nelle composizioni chimiche percentualmente indicate.
SiO₂ | 43,0 -47,5% |
Al₂O₃ | 11,0 – 13,5% |
Fe₂O₃,FeO | 11,0 – 13,5% |
MgO | 9,5 – 12,5% |
CaO | 10,0 – 12,5% |
TiO₂ | 1,0 – 3,5% |
Na₂ | 1,5 – 3,5% |
K₂O | 0.5 – 2,0% |
P₂O₅ | 0,5 – 1,5% |
SO₃ | 0,0 – 0,2% |
H₂O | 0,5 – 2,0% |
Proprietà di base | ||
---|---|---|
Durezza Mohs | EN 101 | min. grado 8 |
Massa volumica | EN 993-1 | 2.90-3.00 kg/m3 |
Assorbimento d’acqua | EN ISO 10545-3 | 0% |
Resistenza a compressione | EN 993-5 | min. 300-450 MPa |
Resistenza alla flessione | EN 993-6 | min. 45 MPa |
Coeff. Dilatazione termica lineare | EN ISO 10545-8 | max. 8.10-6K-1 (0-100°C) |
max. 9.10-6K-1 (0-400°C) | ||
Solubilità all’acido solforico | EN 993-16 | max. 9% della massa |
Sodio idrossido insolubilità | CSN 72 5122 | min. 98,6% della massa |
Resistenza all’abrasione | DN 52108 | max. perdita di 5 cm3/50 cm2 |
Resistenza all’abrasione profonda | EN ISO 10545-6 | max. perdita di 110 mm3 |
Resistenza agli sbalzi termici | DIN 52313 | min. 150 °C |
Resistenza al gelo | EN ISO 10545-12 | da -15 a +15 °C)(min. 50 cicli) |
Altre proprietà | ||
---|---|---|
Porosità apparente | EN 993-1 | 0% del volume |
Conducibilità termica | EN 993-14 | 1,9-2,2 Wm-1K-1 |
Modulo di elasticità | ON 70 1807/67 | nella norma (da 20 a 1.000 °C) |
Resistenza all’isolamento | CSN 34 1382 | min. 11.104 MPa – max. 1010 Ω |
Resistenza allo scivolamento | DIN 51130 | mattonella liscia R10 |
mattonella a rilievo R11 | ||
Radioattività | Ra226 Th228 | 20,8+- 3,4 Bq.kg-1 |
Durezza Vickers | EN ISO 6507-1 | 700-800 HV (MPa) |
Resistenza all’abrasione | DN 52108 | max. perdita di 5 cm3/50 cm2 |
Resistenza all’abrasione profonda | EN ISO 10545-6 | max. perdita di 110 mm3 |
Resistenza agli sbalzi termici | DIN 52313 | min. 150 °C |
Resistenza al gelo | EN ISO 10545-12 | da -15 a +15 °C)(min. 50 cicli) |
La posa può essere eseguita sia con adesivi che con malta cementizia. Per la posa ad adesivo si possono usare quelli che garantiscano il 100% di adesione e consigliati dal fabbricante. Per la posa a sabbia e cemento hanno dato ottimi risultati la malta fatta con sabbia e cemento Portland. Si consiglia una larghezza della fuga minima di 5 mm. Il taglio delle mattonelle viene eseguito con la tradizionale clipper diamantata ad acqua. La sigillatura delle fughe può essere effettuata solamente quando l’adesivo o la malta si sono completamente induriti, dato che l’assorbenza idrica di queste mattonelle è nulla. La sigillatura delle fughe avverrà quindi mediante l’utilizzo di prodotti speciali cementizi colori grigio o antracite seguendo in ogni caso le istruzioni del fabbricante. Subito dopo la sigillatura delle fughe le mattonelle potranno ancora, se necessario, essere pulite già nella fase di stuccatura togliendo i residui della stessa con spugne adeguate e con un prodotto non acido per eliminare il velo di cemento formatosi sulla superficie, in modo da evitare che il colore perda la brillantezza degli ossidi metallici.
La mattonelle di basalto fuso sono di facile manutenzione e possono essere trattate come tutte le mattonelle ceramiche tradizionali.
È vietato l’uso di prodotti aggressivi come soda caustica, acido muriatico o altri acidi.